Drilling Fluids / Additives
Don’t see the Drilling Fluids you’re looking for? We make several Drilling Fluids
that are not listed here.
Contact To KhavaranParaffin
drilling fluids Products
Table Of Contents
Paraffin Wax
Paraffin Waxes have been used by human kind for many years for various purposes and applications. Paraffin wax has many names and synonyms. The word wax applies to a large number of chemically different materials. Recent changes and technological advances resulted in commercial availability of materials and chemical compositions which have picked up name WAX.
Paraffin wax Properties
Generally, Paraffin wax is unbranched alkanes that Solid at ambient temperature and have melting point range of 52 to 70 degree Celsius. Further, they are Thermoplastic in nature and insoluble in water. Soluble in ether, benzene, and certain esters. Most of chemicals do not affect paraffin wax. Burning readily is another characteristic of paraffin wax. Paraffin wax is excellent material in order to restore heat and also its electrical insulation property is second best comparing all other material.
History of paraffin wax
The Paraffin wax which we known today are discovered in 1850. Since then paraffin wax become more popular as it was burning more cleanly and reliably, and was cheaper to manufacture than any other candle fuel. The only disadvantage was low melting point however, this short coming later eased by addition of additives such as stearic acid and technological advances in oil industry. Paraffin wax manufacturers enjoy a boom in 20th century as demand growth dramatically for this material. It is estimated the global consumption of paraffin wax be around 4.4 million tons annually. Paraffin waxes driven from petroleum also can be distinguished by their degree of refining. Paraffin Waxes with maximum half percent oil content that go through deodorization and/or hydrogenation process are called fully refined paraffin wax. Paraffin waxes with oil content up to 2 or 3 percent oil content are named semi refined paraffin wax and waxes with 3-5% oil content referred to as scale wax.
Manufacturing of paraffin wax
Crude oil is the most important source of paraffin wax. Oil Refineries produce two main streams product category from crude oil; Fuels and lubricants. In production of lubricants, refineries use atmospheric distillation residue as raw material and process it further until finished lubricant product is made. The byproduct of this process is called SLACK WAX which is the raw material for paraffin wax manufactures in order to produce paraffin wax. Slack wax in general is a mixture of Wax and Oil which depend on the origin of material can contain 25% oil content. The other and most advance process of making paraffin wax is by Conversion of natural gas, gasified coal and biomass to synthetic fuels. See the below process flow diagram.
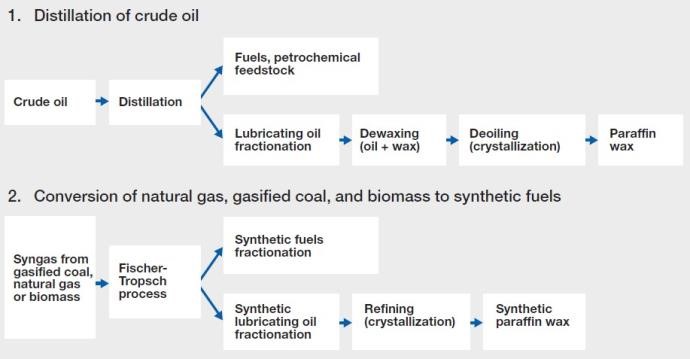
Waxes can be distinguished by their origin as follow:
- Natural waxes
- Mineral waxes
- Synthetic waxes
- Petroleum waxes
It is proven that commercially processing slack wax is more economical compare to conversion of natural gas into paraffin wax. However, recent changes in oil and gas industry and environmental concerns shifted the view of manufacturers to use advance manufacturing process and use natural gas as feedstock. There are several methods which manufactures and refineries can obtain paraffin wax from slack wax. The oldest method is Appling pressure on slack wax in order to separate oil from wax and filter the recovered wax. Finished product of this process is outdated in today’s world but still local manufactures use this process.
Solvent De-oiling Process
Further advancement in paraffin wax industry lead manufacturers to develop Solvent De-Oiling method. In this process Slack wax is heated and mixed with MEK and Toluene and chilled until the Solvent recovers oil; this part called Crystallization. At this point characteristic of paraffin wax such as melting point, penetration and oil content will be controlled by the amount of solvent mixed with slack wax. Crystalized wax is filtered multiple times to separate solvent. Then Crystalized wax will go through solvent recovery plant. At this point the solvent free paraffin wax will send through Decoloring & Deodorizing units in order to separate the remaining impurities and odor removal. Finished product is fully refined paraffin wax. As Solvent Refining process is costly and requires specific and advanced machinery and techniques, manufacturers whom do not have the capital or expertise use Sweating Process.
SWEATING PROCESS
In this process slack wax feedstock is going through the sweating chamber. Sweating chamber is a insulated structure which contains rectangular trays and equipted with screen mesh. Coils and elements are included for cooling and heating purposes. General process steps are as below: First, fresh water is filled in each tray, then feedstock will filled in each tray. Cooling water is circulated through the ducts in order to crystalize wax. Water will be removed and sweating process starts until the paraffin wax reaches the oil connect requirements. The semi-finished paraffin wax will go through further purification process like Decoloring & Deodorizing to make fully refined paraffin wax.
Application Of Paraffin Wax
The most usage of paraffin wax is in candle industry. Wax is also play an important role in hot-melt adhesives, protection of rubber articles (e.g. tires and cables) against premature aging through ozonization, manufacture and impregnation of paper and cardboard . As a constituent of numerous cosmetics (e.g. skin-cream, lipsticks and Vaseline), corrosion preventative or inhibitor (water repellent) and other industries like PVC, agriculture, paint and inks, and etc.
Paraffin Wax Quality Control
Internationally Paraffin waxes quality controlled by their physical properties such as melting point, congealing point, oil content, viscosity, penetration and color. These tests are developed by the ASTM and each has specific number and standard. For further details please visit ASTM website. Clients can use services of international inspectors such as SGS for quality and quantity control purposes
Boints Below Are Schematic Of Paraffin Wax Test
- Melt Point ASTM D87: Provides information on temperature at which most of a given paraffin wax changes from a solid to a liquid.
- Congealing Point ASTM D938: Measures when a paraffin wax ceases to flow.
- Drop Melt Point ASTM D127: Generally used on waxes that don’t show a melting plateau such as petrolatum and microcrystalline waxes.
- Needle Penetration ASTM D1321: Measures the hardness of wax.
- Oil Content ASTM D721: The amount of oil in wax. Indicates degree of refining.
- Kinematic Viscosity ASTM D445: The resistance to flow of a molten wax at the test temperature.
- Color ASTM D6045: Visual comparison of wax color (molten) against glass color standards.